How Are Soccer Cleats Made?
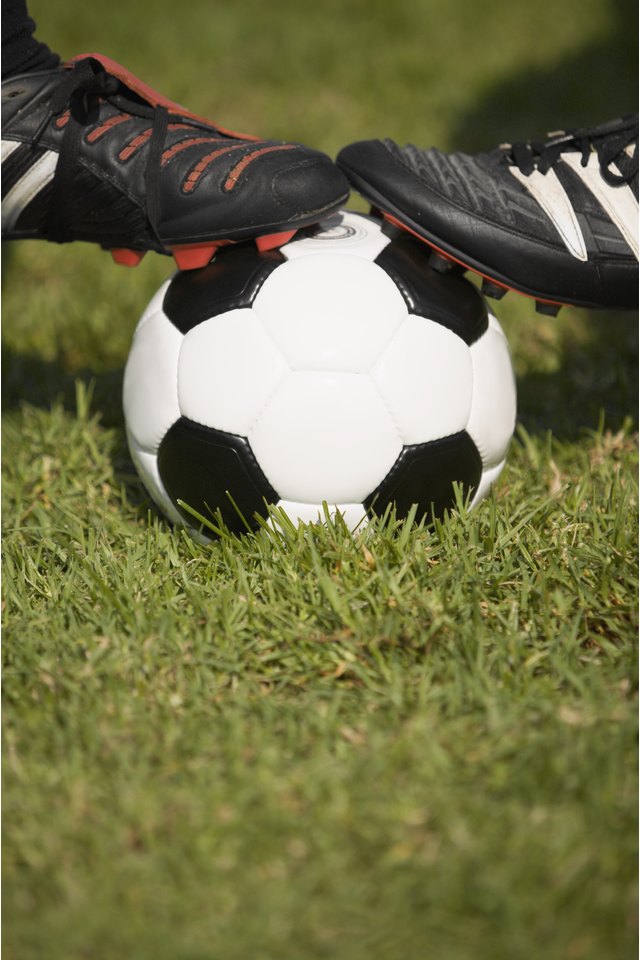
The manufacturing process for a pair of soccer cleats includes the collecting and cutting of the materials; printing and stitching; lasting and assembly; and quality control and packaging. Soccer cleats can go through all the steps of the production process in one day.
Materials and Cutting
The strips of real or synthetic leather are laid out and the patterns of the cleats’ uppers are marked to serve as an outline for cutting. Using metal cookie cutters to shape, a large stamping machine cuts out the pieces of leather, as well as the lining foams of the shoe. Operators cut just one layer of real leather at a time, but can do three to five layers of synthetic leather and lining foams at once. At this point, stitching guidelines, which will serve as direction for stitching lines later on, are sometimes screen-printed onto the cut-out leather. Then, the leather pieces go through a process called skiving, which involves a special machine with a spinning blade that makes the edges thinner to allow for better-looking seams, and that prevents bulging.
Printing and Stitching
Before the pieces of leather are stitched together, any decorative details are screen-printed. The leather is laid out over a printing table and each piece is silk-screened individually. On some models, reflective inks are also printed onto the leather. Some cleats may also feature embossing, an effect created by a machine that produces high-frequency radio waves and pressure to form the material into a particular raised design. After printing and embossing are complete, the leather pieces are brought together to create a shoe through stitching. The leather moves through a factory line, where a succession of workers machine-stitches the parts of the shoe using the previously screen-printed stitching lines as a guide. A hammer is then used to pound the inside seam flat so it doesn't rub on the foot.
Lasting and Assembly
The lasting process gives the cleat its shape. The cleat is first laced up and then a cardboard-type tuck board is positioned and glued to the inside of the bottom of the shoe, where it will eventually sit underneath the liner. Attached to machines, the edges of the upper material are wrapped around the bottom of the cardboard lasting to form the toe, then the heel. The sides of the upper are pulled down tight with either pliers or by hand. The lasting is attached to the outsole, which is the bottom of the cleat. Primer and cement are applied to the outsole and then cured by UV lights, a process that activates the glue. The leather upper is buffed with a small sanding tool, which roughs it around the bottom so that the cement on the outsole can more completely bond to it. A hydraulic press then presses the upper and outsole together. Finally, metal rivets, or the cleats, are inserted..
Quality Control and Packaging
Each of the cleats goes through a quality control process, which consists of a visual check to make sure the right and left shoes match in color, and to catch any excess cement, wrinkles or loose threading. If the cleats are to have hang tags, they're attached to the shoes. The cleats are then wrapped in tissue paper and placed into shoe boxes, where they wait to be shipped for retail sale.
Writer Bio
Kim Nunley has been screenwriting and working as an online health and fitness writer since 2005. She’s had multiple short screenplays produced and her feature scripts have placed at the Austin Film Festival. Prior to writing full-time, she worked as a strength coach, athletic coach and college instructor. She holds a master's degree in kinesiology from California State University, Fullerton.